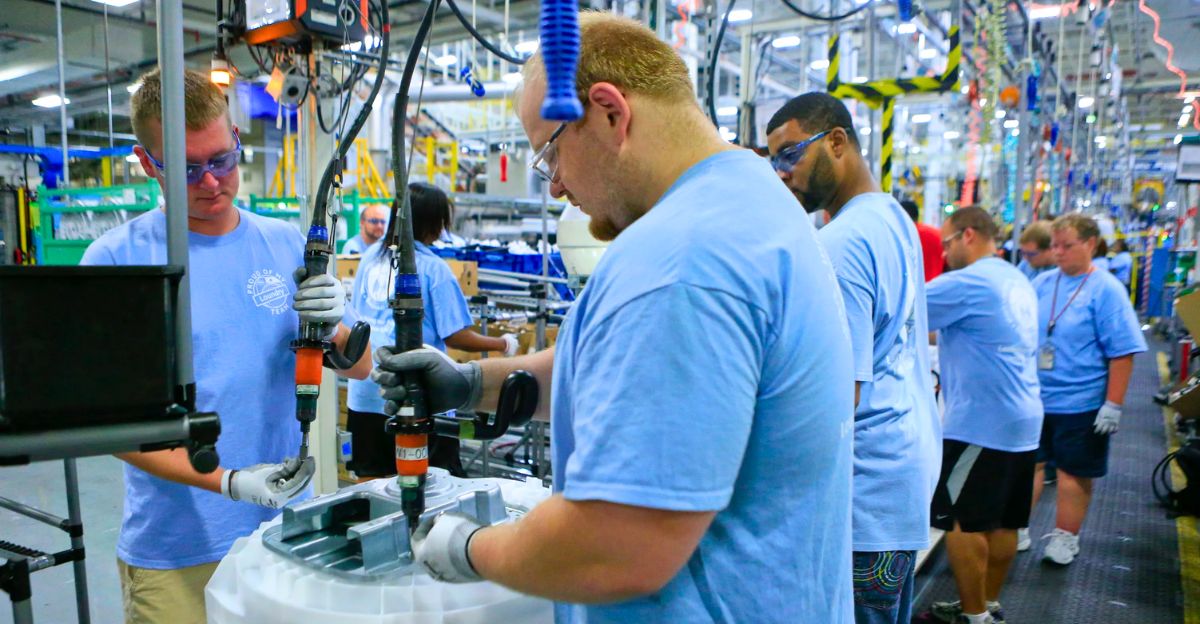
GE Appliances is packing up production in China, and bringing it back to Kentucky. Yep, the same company owned by China’s Haier since 2016 just dropped nearly half a billion dollars to shift operations back to the U.S. That means 800 new jobs in Louisville, 15 washing machine models making the trip home, and a factory big enough to hold 33 football fields.
This isn’t business as usual. It’s a major shake-up. A Chinese-owned brand is now betting against China’s economy and putting its money on American manufacturing. That says a lot about where things are headed.
So what does this all mean; for workers, for trade, and for what “Made in America” even means now? Let’s break it down.
The Tariff Strategy That Changed Everything
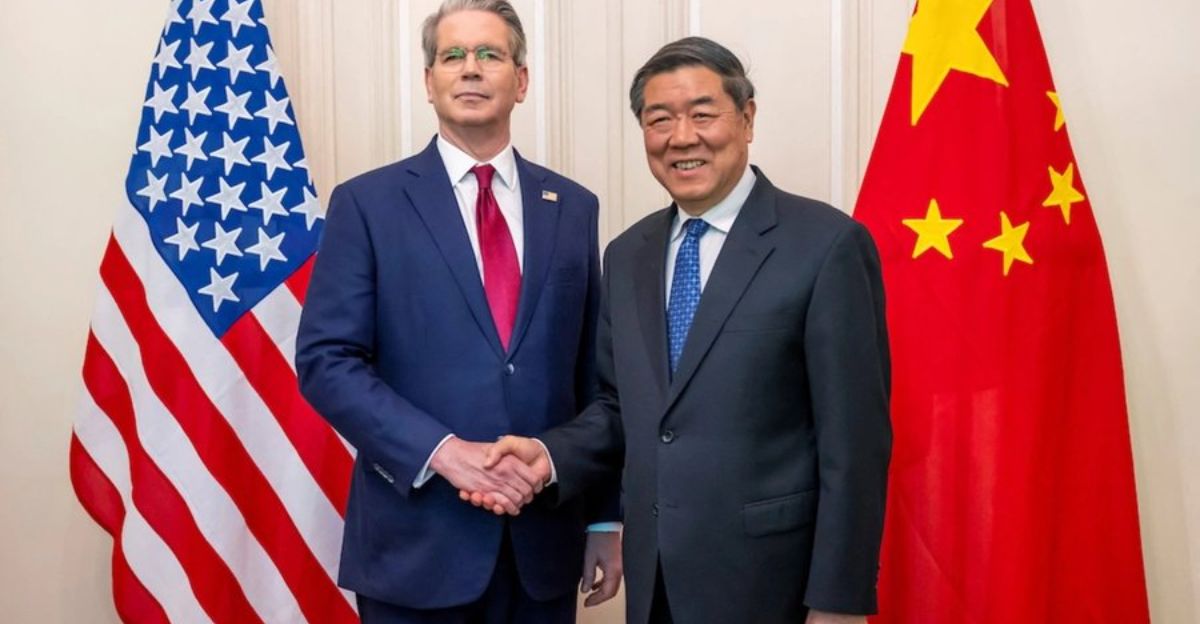
Donald Trump’s return brought sweeping tariffs, and this time, they’re leaving a mark. By June 2025, tariffs on Chinese goods hit 55%, driven by a mix of baseline duties, penalties tied to fentanyl, and Section 301 tariffs. Steel and aluminum alone now face 50% levies. For appliance makers, that spells rising costs and shrinking profits. GE Appliances, owned by China’s Haier, saw the writing on the wall.
Even though plans to reshore began earlier, CEO Kevin Nolan admitted the tariff storm “added a sense of urgency.” Suddenly, China wasn’t just expensive, it was untenable. So Haier bet big on something new: building machines where they’ll be sold.
Inside Kentucky’s 750-Acre Comeback Zone
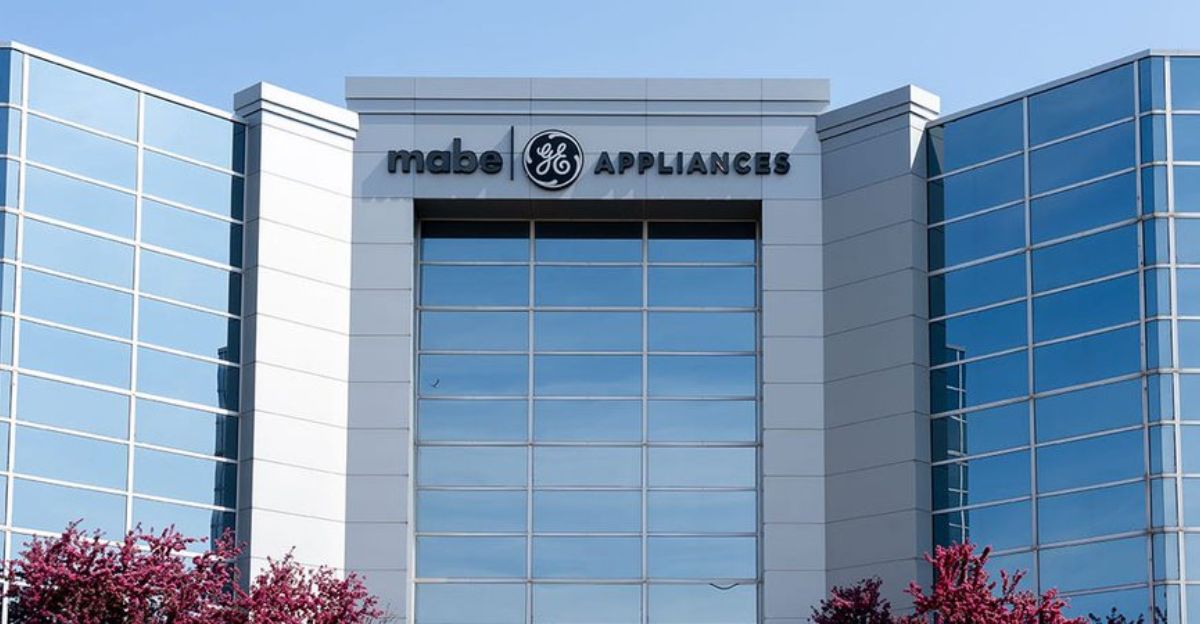
Louisville’s Appliance Park is a monument to American industry, and now it’s being reimagined. Once home to 25,000 workers, today’s streamlined workforce of 8,000 is building smarter, not just bigger. GE’s new investment brings advanced robotics, autonomous vehicles, and AI into play, far from the 1950s assembly lines of old.
CEO Kevin Nolan describes it as a “zero-distance” model, where innovation and production are tightly connected. With Kentucky adding 3,300 manufacturing jobs in a single month, the state is quietly becoming a hotspot for industrial revival.
Why Distance No Longer Makes Economic Sense
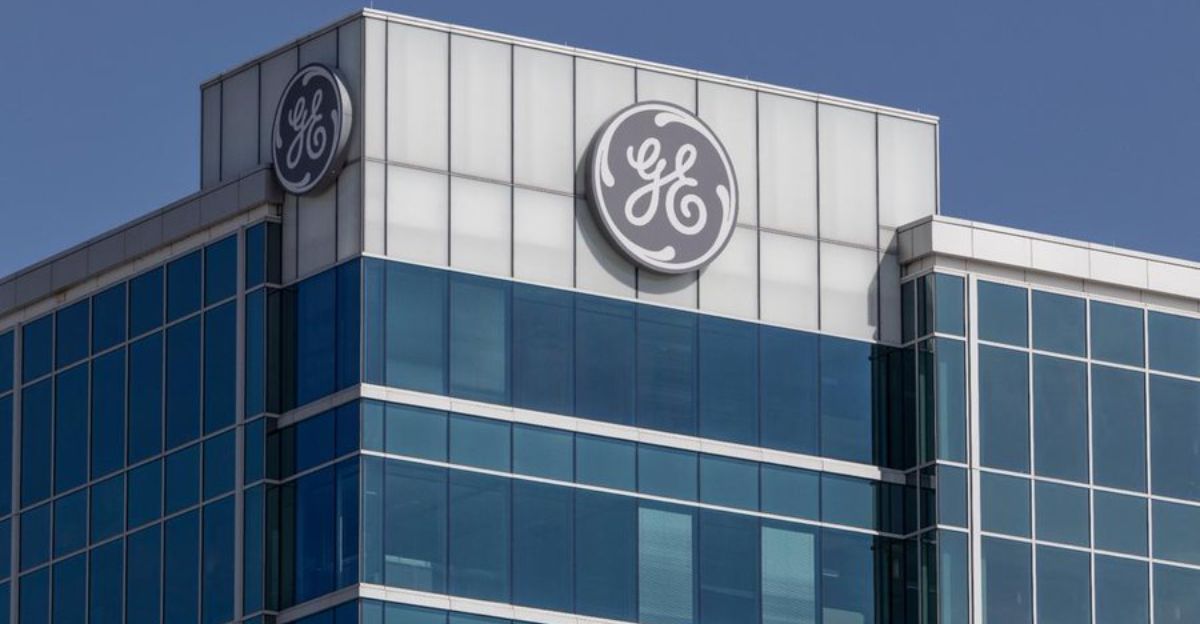
Offshoring once ruled global manufacturing logic, cheap labor, distant factories, and long timelines. But GE’s “zero-distance” model flips that idea. Proximity to U.S. customers means faster feedback, tighter collaboration between design and production, and less vulnerability to geopolitical or shipping chaos.
Labor may be pricier, but reliability and innovation now outweigh savings. In fact, GE isn’t alone. The Reshoring Initiative tracked 244,000 U.S. jobs announced in 2024 alone. Companies are realizing that domestic production isn’t just patriotic, it’s pragmatic. As global risks rise and expectations tighten, manufacturing close to home is emerging as a smarter play, not a sentimental one.
Why Even a Chinese Giant Is Leaving China
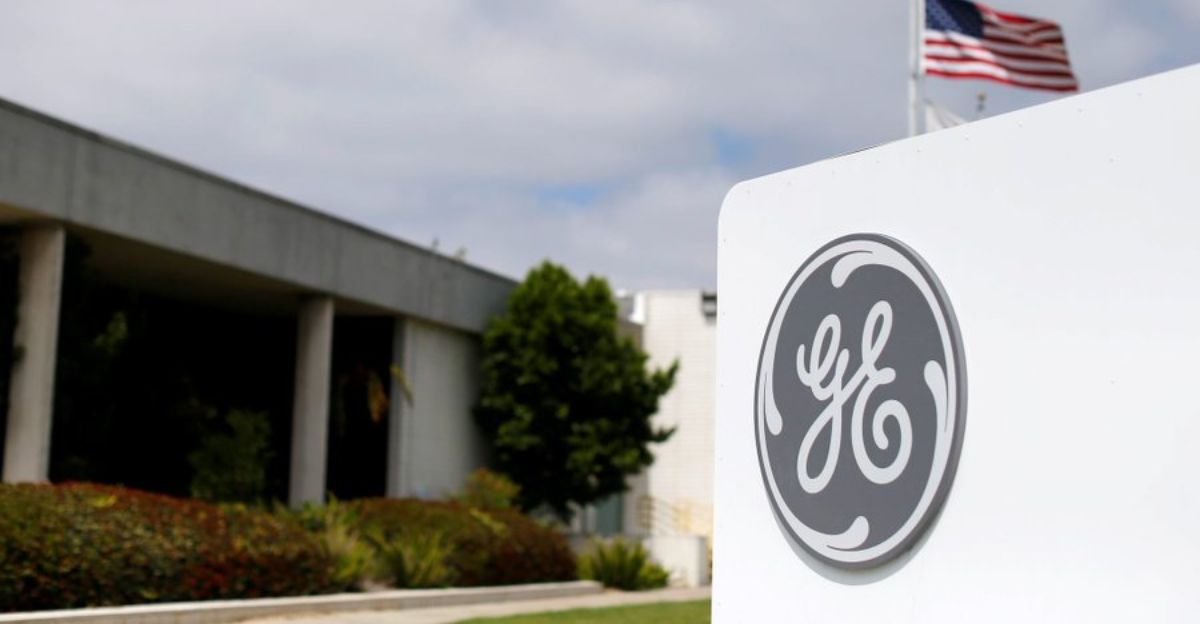
Haier’s story defies expectations. As the world’s largest appliance maker, the Chinese conglomerate built its U.S. success not through exports, but by buying GE Appliances in 2016. Today, Haier holds nearly 27% of the U.S. market, ahead of Whirlpool. But instead of expanding Chinese output, it’s doubling down on American soil. The reason? Brand trust, customer preference, and a growing belief that U.S. consumers respond better to products made locally.
Even for a Chinese firm, “Made in America” carries more weight. Haier’s move is less about abandoning China and more about recognizing where long-term growth, and loyalty—, really come from.
Steel and the New Supply Chain Advantage
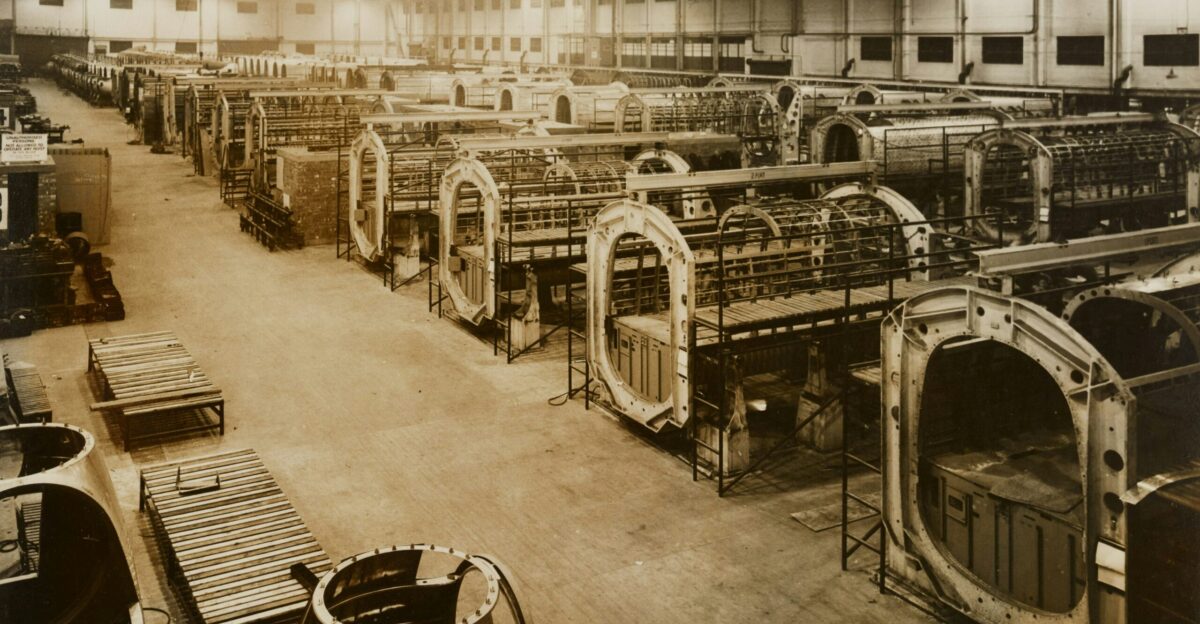
Steel is a core ingredient in washing machines, and Trump’s tariffs have turned it into a geopolitical flashpoint. Foreign steel is now too expensive to justify. GE responded by sourcing nearly all its steel domestically. That shift is about control. U.S.-based supply chains are proving more resilient and more secure amid global instability.
By moving closer to American suppliers, GE minimizes disruption risks and strengthens its production model. The broader takeaway? Tariffs are doing what they were designed to do: pulling supply chains home and giving domestic steelmakers a new lease on life.
Why 800 Jobs Still Matter
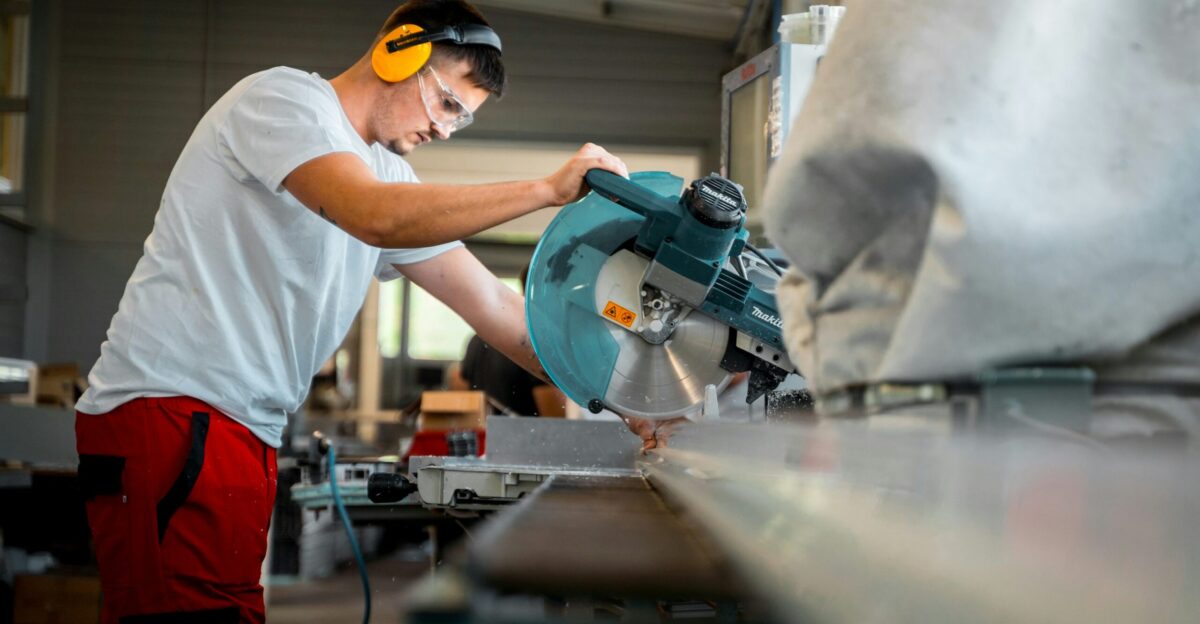
In a workforce of over 170 million, 800 jobs may not sound like much. But in Louisville, those roles carry weight. Manufacturing has the highest economic ripple effect of any sector, every dollar spent creates nearly three more across the economy. These aren’t gig jobs or short-term contracts, they’re stable, full-time roles with room to grow. Many don’t require a college degree, yet they offer pathways to middle-class stability.
For a Chinese-owned company to invest in American labor speaks volumes. It’s a validation of U.S. manufacturing skill and a reminder that reshoring isn’t abstract; it changes lives, one job at a time.
The Fight for Appliance Supremacy Just Got Real

GE Appliances isn’t just reshoring, it’s preparing for battle. With this move, it’s vying to become the top U.S. washing machine maker, squaring off against Whirlpool, Samsung, and LG. Each rival brings something different: Whirlpool leans into heritage, Samsung pushes AI, LG bets on smart homes. GE’s strategy? Chinese funding, American credibility, and a new wave of domestic production.
By blending global resources with local presence, GE could carve out a powerful middle lane. As tariffs reshape the market, the winners will be companies agile enough to adapt, and bold enough to build where they sell.
The Strange Power of the “Made in America” Label
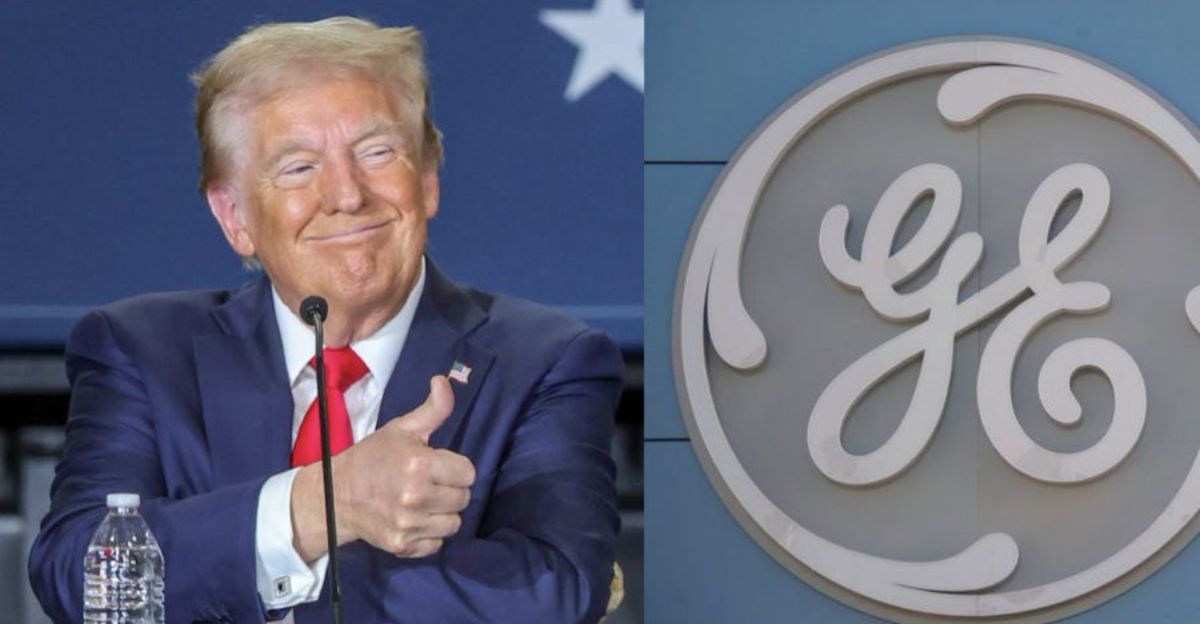
Americans say they want to support local products, yet they often buy the cheapest option. GE’s gamble banks on closing that gap. Appliances, unlike t-shirts or gadgets, are emotional purchases tied to home life and reliability. When pricing gets closer, trust and perception take the lead. Haier understands this tension.
By reshoring GE’s production, it aligns consumer psychology with economic reality, making the purchase feel better, not just smarter. That matters in a market where brand loyalty isn’t just about performance, but also pride. This shift helps resolve the quiet contradiction many shoppers feel every time they check a label.
This Isn’t Just About GE—It’s a National Trend
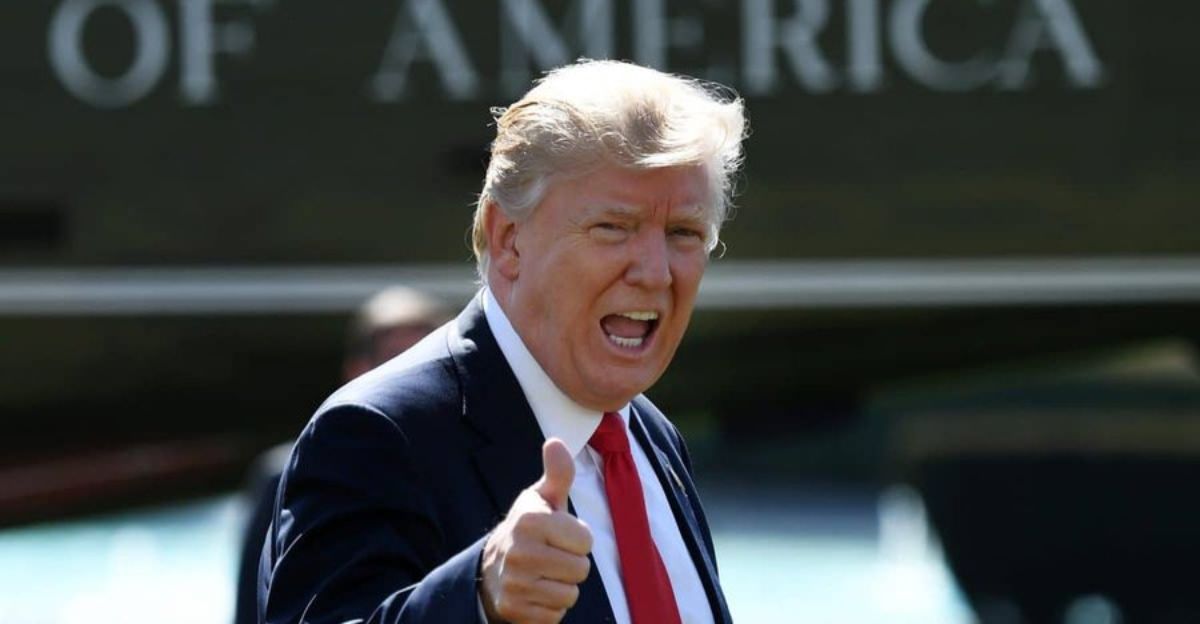
GE is part of something bigger. Reshoring is happening across the board, from semiconductors to autos. In 2024 alone, companies announced nearly a quarter-million new U.S. manufacturing jobs. Since 2010, that figure has topped 1.7 million. What’s driving it? Tariffs, yes, but also reliability, skilled labor, and tighter integration between design, software, and production.
As industries grow more complex, local production becomes less of a luxury and more of a necessity. The result is a reshaping of the entire manufacturing landscape. GE’s return to Kentucky is one headline in a wave that’s rewriting the rules of global industry.
Why the Future Factory Is American Made
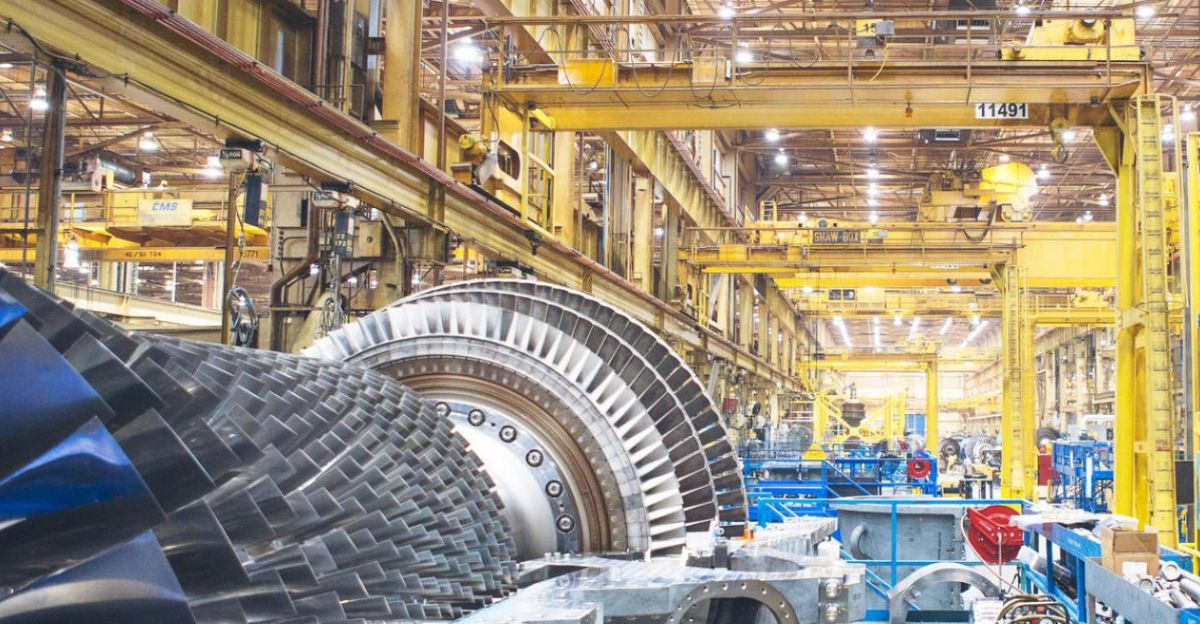
Forget the old image of loud, dusty assembly lines. Today’s factories are smart, clean, and fast. Louisville’s upgrade will feature robotics, AI, and real-time quality control, tech that needs skilled labor and advanced infrastructure. Kentucky’s long industrial history gives it an edge, with engineers, suppliers, and schools all feeding into the system.
When Haier chooses the U.S. for its most advanced plant, it signals a major shift: the best place to innovate isn’t necessarily the cheapest. It’s where the talent lives. Manufacturing isn’t just coming back, it’s evolving. And it’s doing so in places built to compete, not just survive.
Rethinking What “Made in America” Really Means
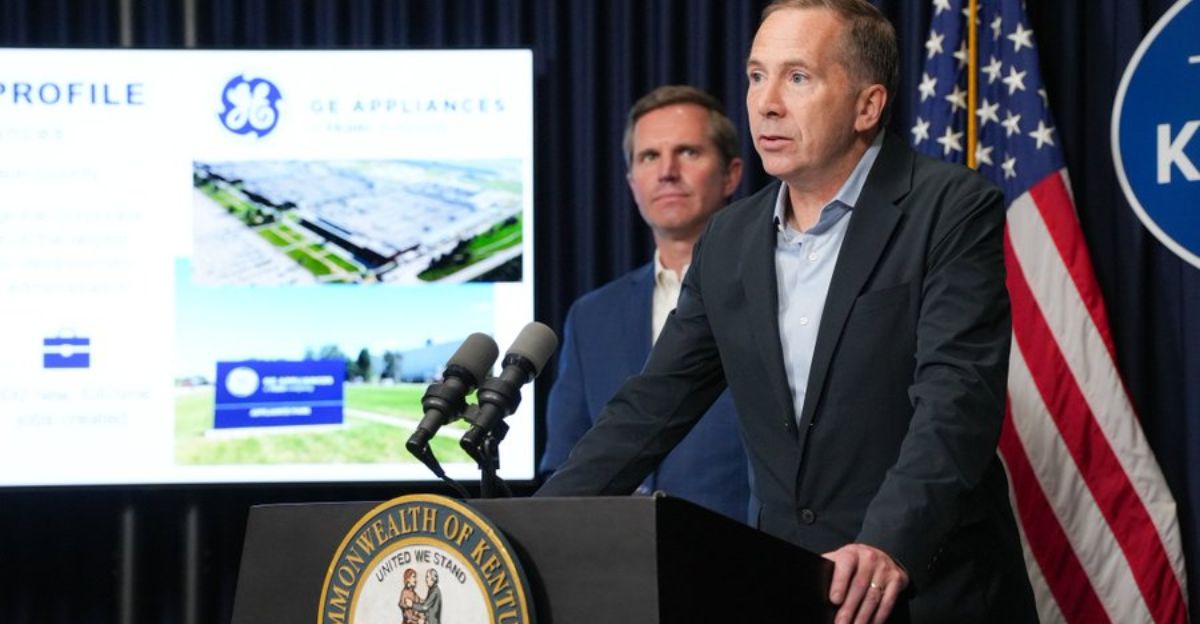
GE’s decision to move production back to Kentucky shows how economics, psychology, and policy are reshaping the global map. It’s not just about tariffs or jobs, it’s about trust, speed, and control.
As more companies rethink distant supply chains, the value of local production grows. What once seemed nostalgic now feels strategic. Manufacturing in America isn’t a step backward, it’s a step into a new kind of competitiveness.
From consumers to CEOs, the appetite for proximity is growing. And while the headlines focus on jobs or tariffs, the real story is about resilience. The smartest factory might just be the one closest to home.